Question answered in Quora - In the warehouse picking how can you prove the ROI on employees many ca
- puga2006
- Apr 9, 2016
- 2 min read
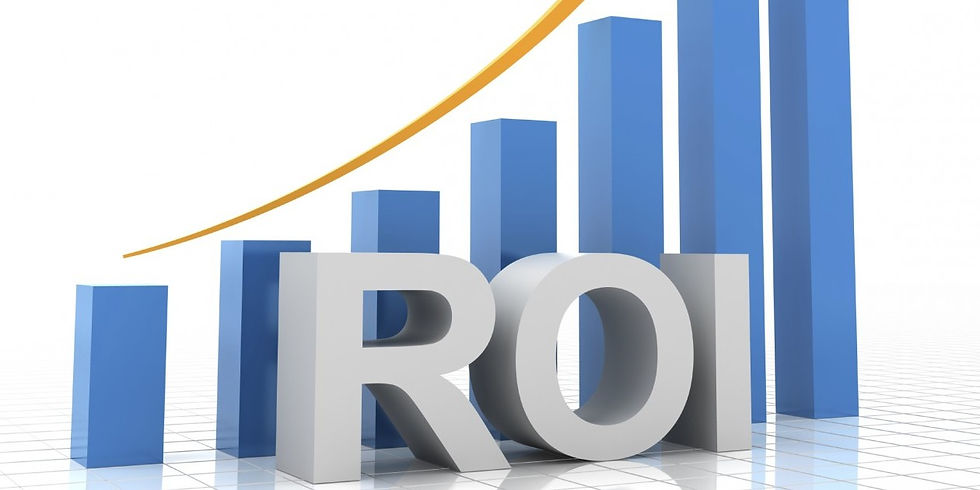
Here are three ways that can be done
1 - Measure your mispicks at the picker level. The WMS you are using might have a Mispick Report. Or you could create one, usually based on Returns that are coming back, because the customer is returning the product because that is not the product they ordered. So you need to match up the Returns with the original Carton# and then create a mispick report and narrow down to the picker that made that mis pick or back order. Once that measurement starts happening the pickers will pay much more attention, so mispicks will reduce
2 - Do not provide the picker, the ability to Back order (or out of stock) in the picking function. Train the pickers to always go to a Supervisor to be able to do back order. So the supervisor will double check the back order scenario, make sure there is absolutely no product within the 4 walls of the warehouse before back ordering the product
3 - Institute an Audit process for a certain % of the cartons, especially if there is a back order scenario, usually this is done by weight, if the weight difference is much higher than a tolerance % then that carton will be chosen for Audit. Once that carton is identified then that can be narrowed down to a specific picker
Once the # of mispicks are identified and the time spent on resolving this (many people's time) are identified then you can measure the amount of labor spent on resolving that situation. So given that this much time & dollars are wasted on mispicks, hiring better pickers will cost X dollars extra, however this is how much the company will save due to not having to spend time on troubleshooting how these mispicks originated in the first place.
Also check out my book Puga Sankara's Supply Chain Blog - that is a must read before spending Hundreds & Thousands of $$$ on your MBA or Masters Degree to get the best ROI or before starting your Entrepreneurial journey.
Comments